Instrumentation & Control: the brain and central nervous system of the plant
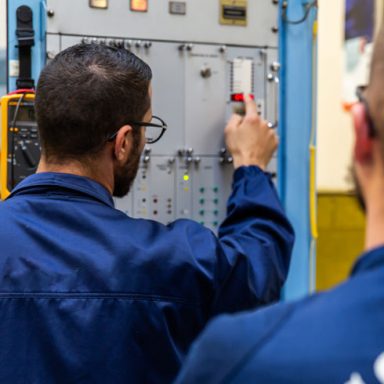
Training facilitator in practical session with trainees. © Framatome, Mathieu Berenger
Managing the different systems necessary for a nuclear power plant to operate requires precise, reliable control. This is provided by the instrumentation and control system.
The I&C system is the brain and central nervous system of the power plant. Its purpose is to secure the production of electricity in a safe and controlled environment.
The instrumentation and control systems are adapted to the design of each reactor, the needs of utilities and the standards of the nuclear safety authorities in each country. It’s an extremely elaborate system that measures, monitors, checks, controls, communicates and protects the plant’s operations.
Our teams design, manufacture, install and maintain cutting-edge nuclear Instrumentation & Control (I&C) solutions ensuring the safety, availability and reliability of nuclear power plants throughout the world.
Did you know?
At the center of the I&C system are programmable controllers: these comprise hundreds of cabinets full of electronic equipment that monitors the reactor.
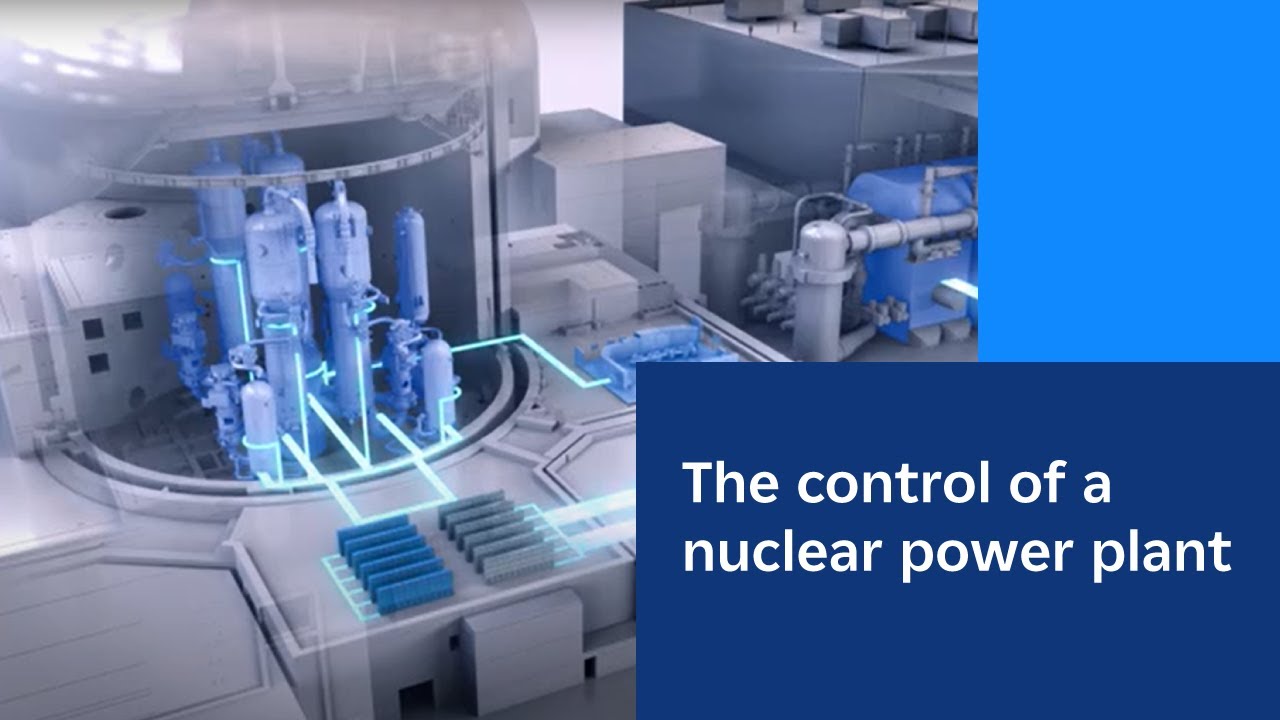
Video: The control of a nuclear power plant
A presenter explains how a nuclear power plant works. During his presentation, his words are illustrated by 3D animations of the facilities present in the nuclear reactor. He speaks:
“Have you ever realized how sophisticated a nuclear reactor is? Managing an installation of this size requires precise reliable control. The operators, whose role this is, are assisted by an essential component of the power plant: the instrumentation and control system.
Its mission is to ensure the safe production of electricity. And when we say safe we are talking about:
- the safety of the reactor itself,
- safety of people
- and safety for the environment.
The instrumentation and control system is the brain and nervous system of the plant.
At the center of the instrumentation and control system are programmable controllers. These comprise hundreds of cabinets full of electronic equipment that monitors the reactor. The programmable controllers receive a constant stream of information about the plant’s activity from thousands of sensors. There are all kinds of sensors monitoring:
- temperature,
- pressure,
- flow rate,
- voltage,
- chemical concentration
- and so on.
Several times per second tens of thousands of signals from these sensors are analyzed and processed by the programmable controllers which can then take corrective action if necessary. Because in turn a programmable controller can change how the reactor operates through what are known as actuators. These include devices such as valves, pumps, fans, motors.
There are two groups of programmable controllers in a nuclear plant:
- operational controllers which make sure that the reactor is operating correctly
- and safety controllers which take control of the plant if an anomaly is detected.
Say for example that there’s a drop in water pressure in a pipe. The operational instrumentation and control system will order one or more valves to open returning the pressure to its correct level. But if this does not work, if the pressure does not return to normal and the problem worsens. It is the safety controllers that take control of the reactor. They have only one aim to prevent an accident. They will order the emergency shutdown of the reactor. To shut down the reactor, they cause the control rod clusters to drop. These clusters are made up of rods that enter the reactor vessel within two seconds and stop the reactor. The rods are made from absorbent materials able to stop the chain reaction. The safety controllers then initiate all the operations needed to stabilize and secure the reactor.
All these actions whether linked to operation or safety are monitored by operator technicians nothing escapes their watchful eye in the control room which provides the interface between man and machine. They monitor the state of the plant in real time thanks to the data processed sorted and analyzed by the instrumentation and control system. Sitting at their consoles, they have all the tools necessary to monitor, analyze, compare, check and above all anticipate.
This control room is therefore a data center decision making center and control center all rolled into one. The technicians can take control at any moment and have all the equipment needed to control the various systems remotely.
The instrumentation and control system of a nuclear plant meets extremely rigorous safety requirements. These requirements form part of plant design which is based on two principles.
The first is diversity. We want to make sure that the different pieces of instrumentation and control equipment do not all fail at the same time due to their similarity. So we use several different methods to measure the same parameter. For instance, to check that the water is the right temperature, we use a temperature sensor but also a pressure sensor. This is what we mean by diversity and this applies to all our equipment.
The second important principle is redundancy. All sensors controllers and actuators together form a complete system known as a safeguard train. Each reactor has at least two different safeguard trains and sometimes three or even four for an EPR reactor in case one is unavailable. In addition these trains are physically separate from each other in isolated buildings to ensure, for example, that a fire affecting one train does not damage the others. They are also electrically separate each train has its own power supply.
The instrumentation and control system must be adapted to:
- the design of each reactor,
- the needs of utility companies
- and the standards required by the nuclear safety authorities in each country.
The instrumentation and control system is extremely elaborate. Its mission is to:
- measure,
- monitor,
- check,
- control,
- communicate
- and protect.”
Meeting our customers’ needs
Tried-and-tested and representing the cutting edge in technology, our products and solutions address our customers’ main requirements to include:
- Enhance safety
- Enable performance gains
- Increase long-term flexibility
- Reduce costs
- Extend the plants operating life
News
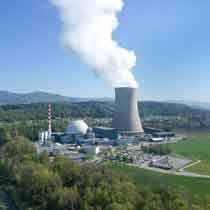
Framatome to modernize instrumentation and control system of Swiss nuclear power plant
Solutions portfolio
440+
I&C systems installed
on all types of reactors
200+
instrumentation
systems in operation
190+
simulators delivered
over the past 30 years
A full range of I&C solutions
For new build projects, Framatome supplies programmable controllers and instrumentation solutions which meet all the requirements in terms of safety, security and performance.
For modernization projects, Framatome offers fully digital systems, wired systems or an optimized combination of both.
Framatome also provides solutions for the design of various actuation systems capable of meeting the highest safety class and autonomous systems such as refueling machines, safety-related auxiliaries or lifting equipment.
Safety and adaptability
For power plant modernization or design projects, our solutions can be adapted to all types of reactors and meet stringent safety and security standards.
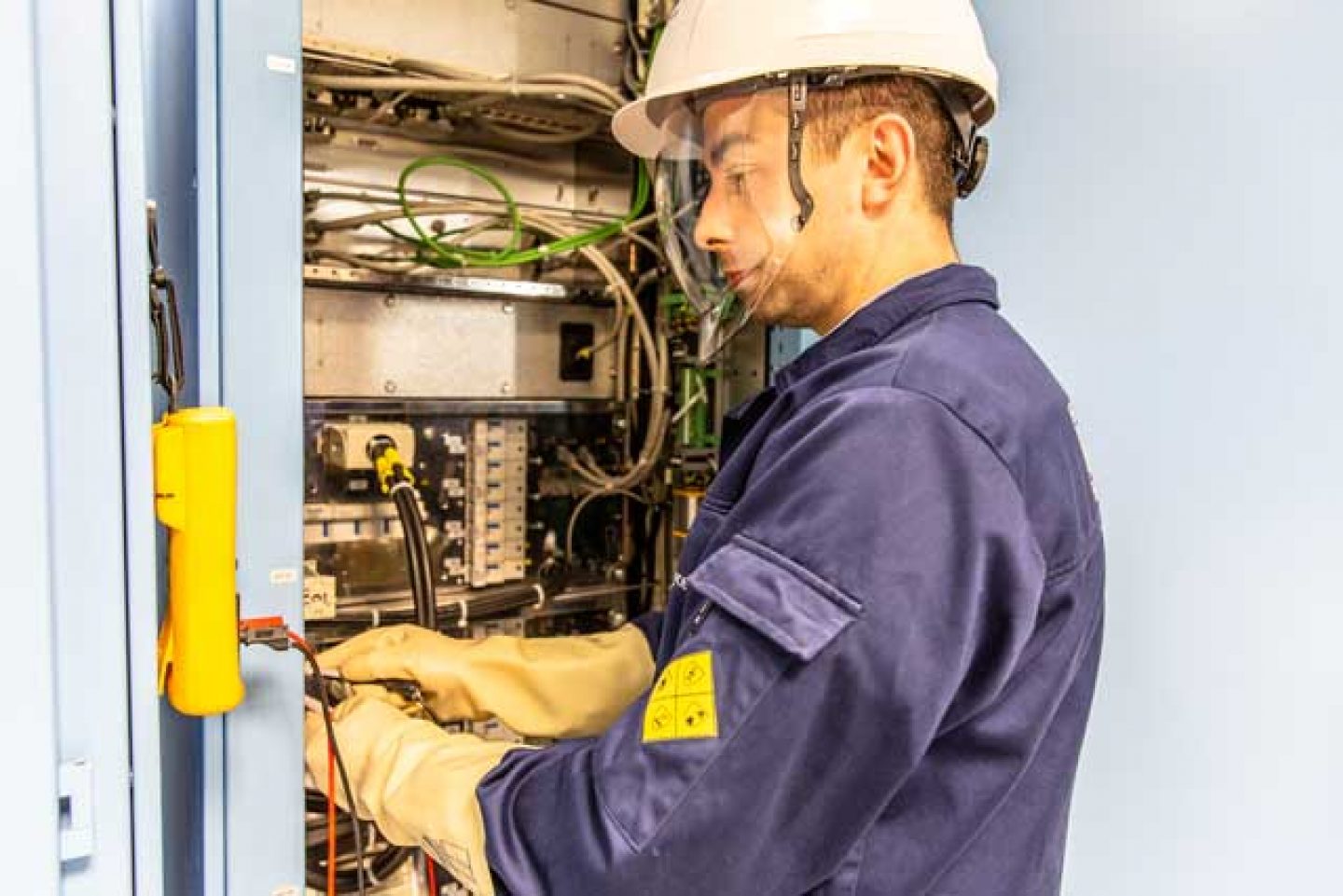
Technician perfoming functionel tests on electroniques boards. © Framatome, Mathieu Beranger
International expertise in engineering
The architecture of the I&C system is a key element in the success of new power plant projects.
With our comprehensive in-house engineering expertise, we cover the whole I&C engineering lifecycle system from feasibility studies through factory acceptance testing and commissioning users achieve optimum I&C systems performance.
Assistance from design through to installation…and more
With over 60 years’ experience, we offer our customers solutions which are adapted to their needs throughout the life cycle of their facilities, with a broad range of services that stretch from the design phase through to the commissioning of I&C systems and long-term support.
Framatome offers modernization solutions that integrate seamlessly into existing systems, save on costs and extend the life of plants. Our teams also manage spare parts, systems maintenance, management of obsolescence and training.
We understand the requirements of nuclear energy generation and the speed at which the market evolves. We continually develop new solutions and skills in I&C to provide our customers with even more added value, such as expertise in cybersecurity, digital solutions, solutions for small modular reactors and 4th-generation reactors.
Did you know?
Safety authorities may require diverse analog back-up systems for the digital safety I&C systems of new build plant projects. Framatome’s analog solutions are built as separate sub-assemblies and readily available. These products make it possible to have a diverse actuation system for high-safety class equipment.
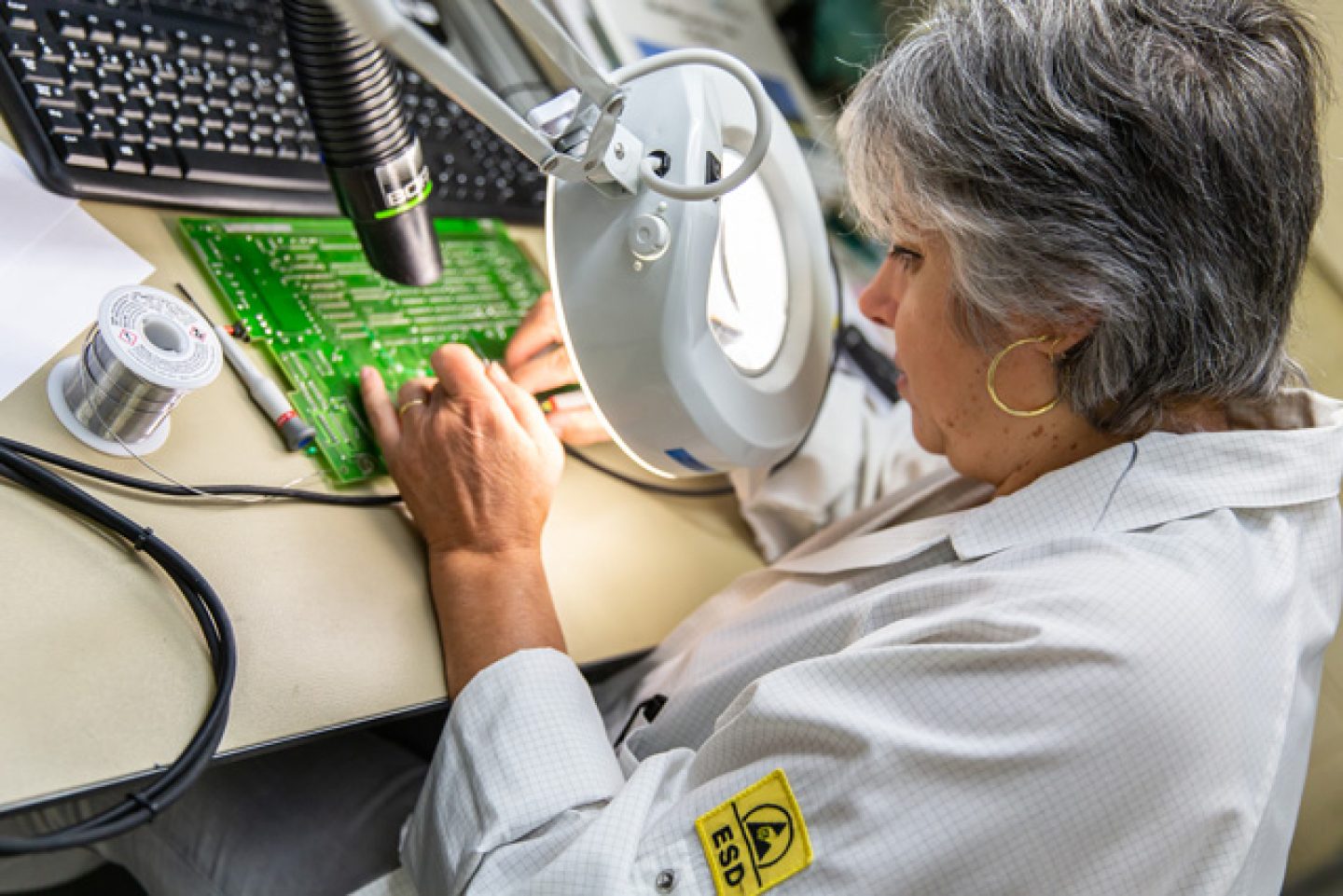
Manufacturing and repair activity of electronic boardss © Framatome, Mathieu Berenger