Robots now vital assistants in the nuclear sector
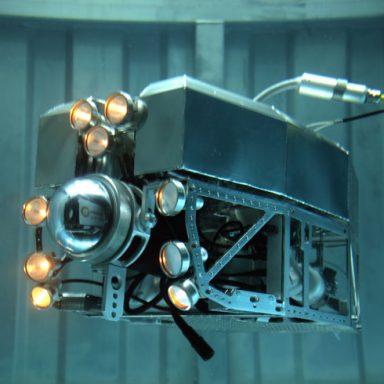
Susi, submarine and remote controlled inspection tool for nuclear services © Areva
They go by names such as Charli, Eloise, Pelican or Forerunner and they’ve joined the ranks at Framatome to lend their iron hands to our teams and our customers’ teams.
These robotic collaborators significantly improve safety in the field and enhance the performance of operations. They are the illustration of our innovation approach, aiming to offer safe and increasingly competitive nuclear energy.
Driven by major technological advances, these robots represent years of productive, collective research and development. Experience some of this innovation in action: from the Saint-Marcel plant, where operators use robotic arms to facilitate strenuous work and reduce occupational risk, through to dismantling of the Superphénix reactor, where the laser robot Eloise has become quite simply… indispensable.
ECAM Challenge – Leveraging collective intelligence to come up with disruptive solutions
Industrial innovation has increasingly required appealing to open ecosystems and schemes. Framatome has for instance taken part in the 2018 Fest’Innov contest from the Catholic School of Arts et Métiers of Lyon. Coached by a Framatome expert, a group of students has racked their brains during 24 hours, to propose a solution to one of our industrial technical challenge: pipe cutting for nuclear dismantling.
Framatome has thus been able to take advantage of the external point of view of future engineers that have always been nurtured by new technologies and uninhibited. The group diversity which mixed technical and business profiles was a key success factor in the emergence of disruptive innovation leads.
Reciprocally, the students had the chance to discover the nuclear and the industry employment opportunities. They enjoyed envisioning how stimulating solving our everyday challenges and working in our industry are, which surely is one of our sector’s major attraction factor.
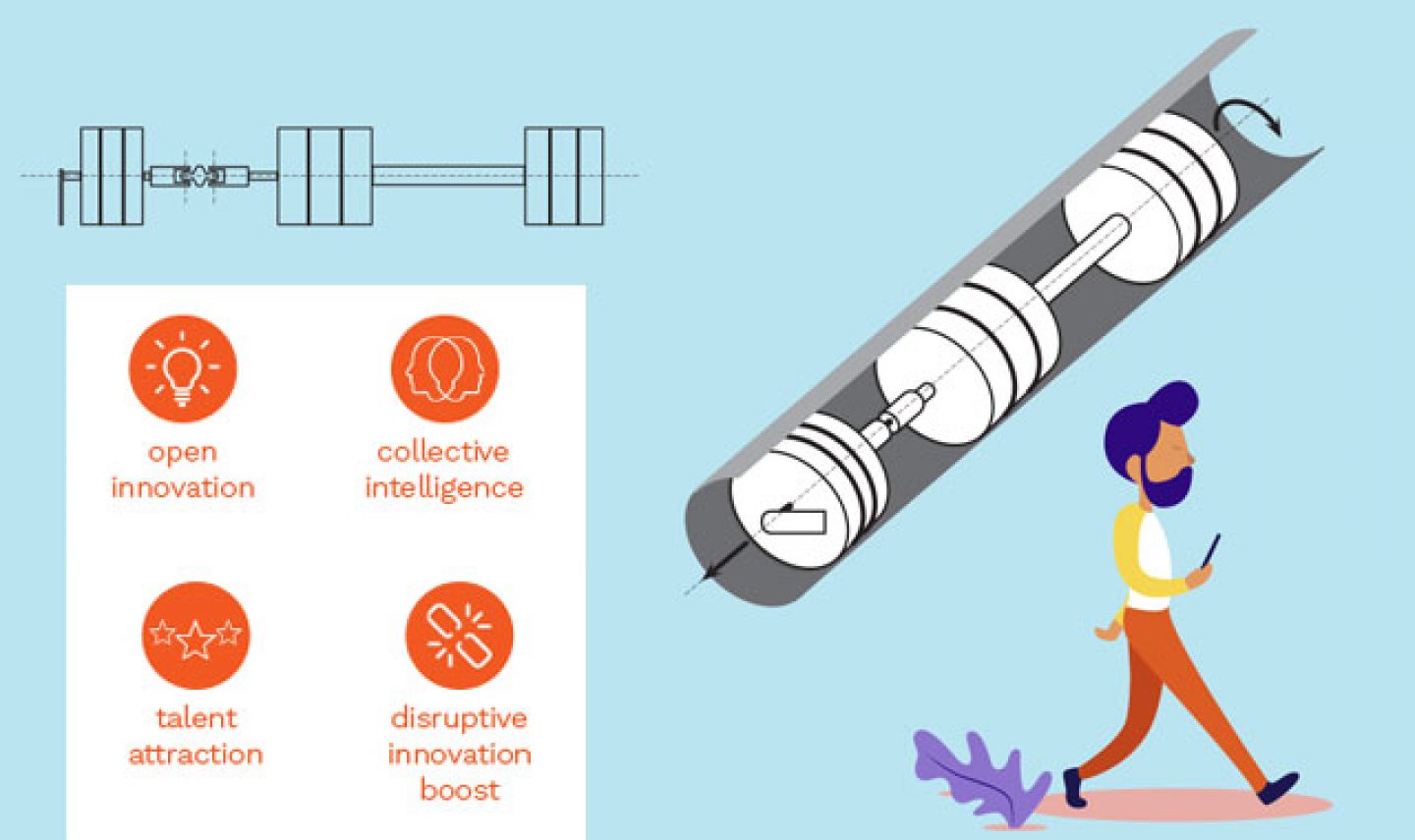
ECAM Challenge
SUSI – A robotized submarine system for inspections
Available in a variety of models, SUSI can examine most reactor coolant system components as well as reactor pressure vessel, reactor pressure vessel head, pumps, pressurizers and piping in nuclear power plants worldwide.
SUSI also performs visual ultrasonic inspections of baffle bolts. Plus, it can serve as a gripping device to retrieve foreign objects. In addition, the robot can be calibrated under water at any time during the inspection.
A separate satellite camera system can be deployed with SUSI or on its own to further enhance inspection results in hard-to-reach areas.
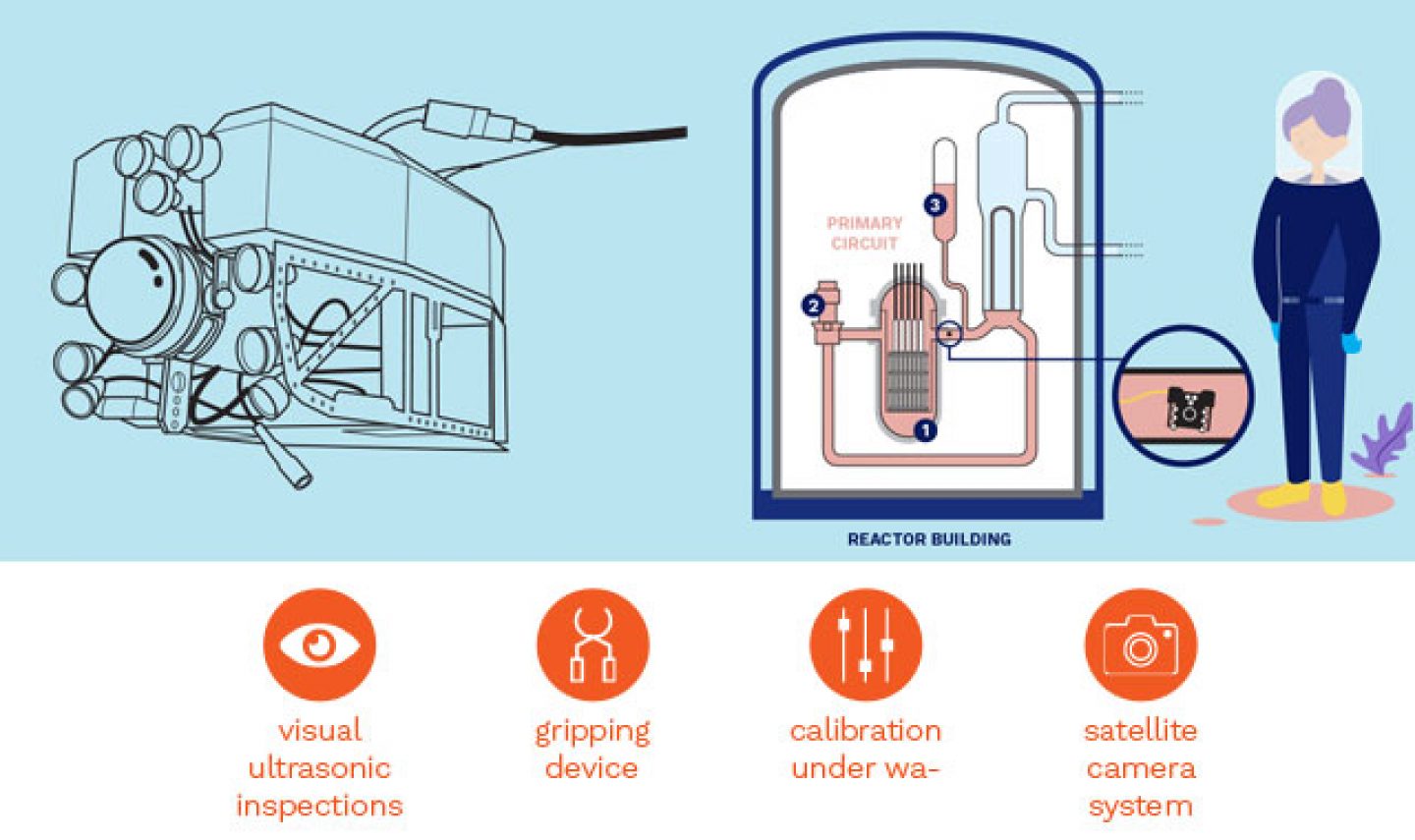
Susi
Pelican for foreign material extraction
PELICAN is a device that allows the extraction of foreign material potentially present in the fuel assemblies, whatever its position.
After a very fast installation of 30 minutes, the robot is able to extract foreign material on fuel assemblies in less than 15 minutes.
Totally safe and controlled to use, PELICAN avoids any damage to the fuel assemblies. Its reduced dimensions make it easy to be transported directly to the fuel building through the auxiliary building.
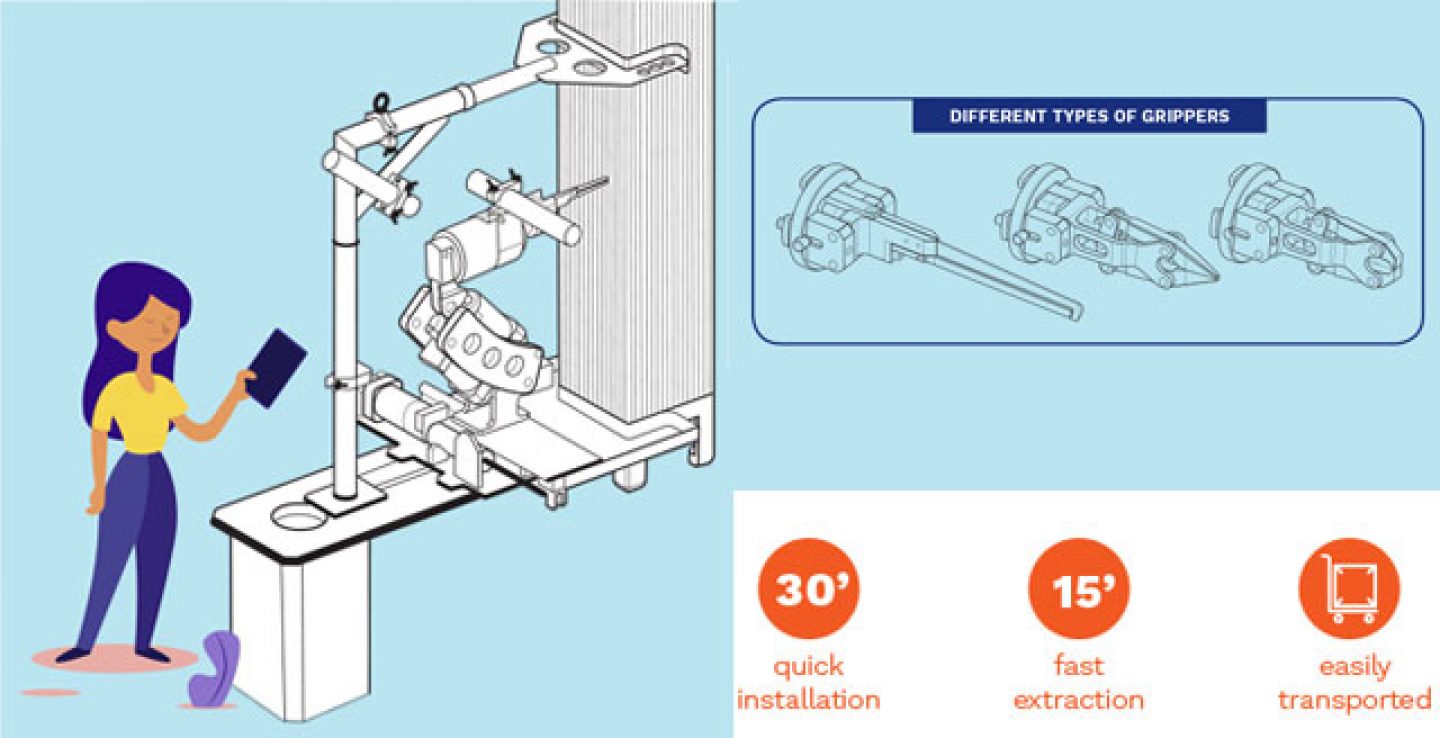
Pelican
Cobotics – The first right hand of operators
Saint-Marcel facility’s “process development” team proposed a cobotics development program, i.e. use of robots assisting in operations performed by operating personnel. A cobot has thus been installed in the Processes room of the plant. It’s a robotic and articulated arm piloted by an operator.
With this cobot, the objective is to reduce the drudgery and the risk of musculoskeletal problems associated with repetitive actions. The operator’s role is changing to become one of supervision of the operation.
These cobots have the specific ability to develop in the same environment as the human operator with all safety conditions applied, with the required aim of collaboration: humans and machines working together.
Light and flexible, the cobot is compact and easy to move. Adapted to the facility’s fabrications, programming and control are very simple, as the cobot records the movements of the human operator and copies them.
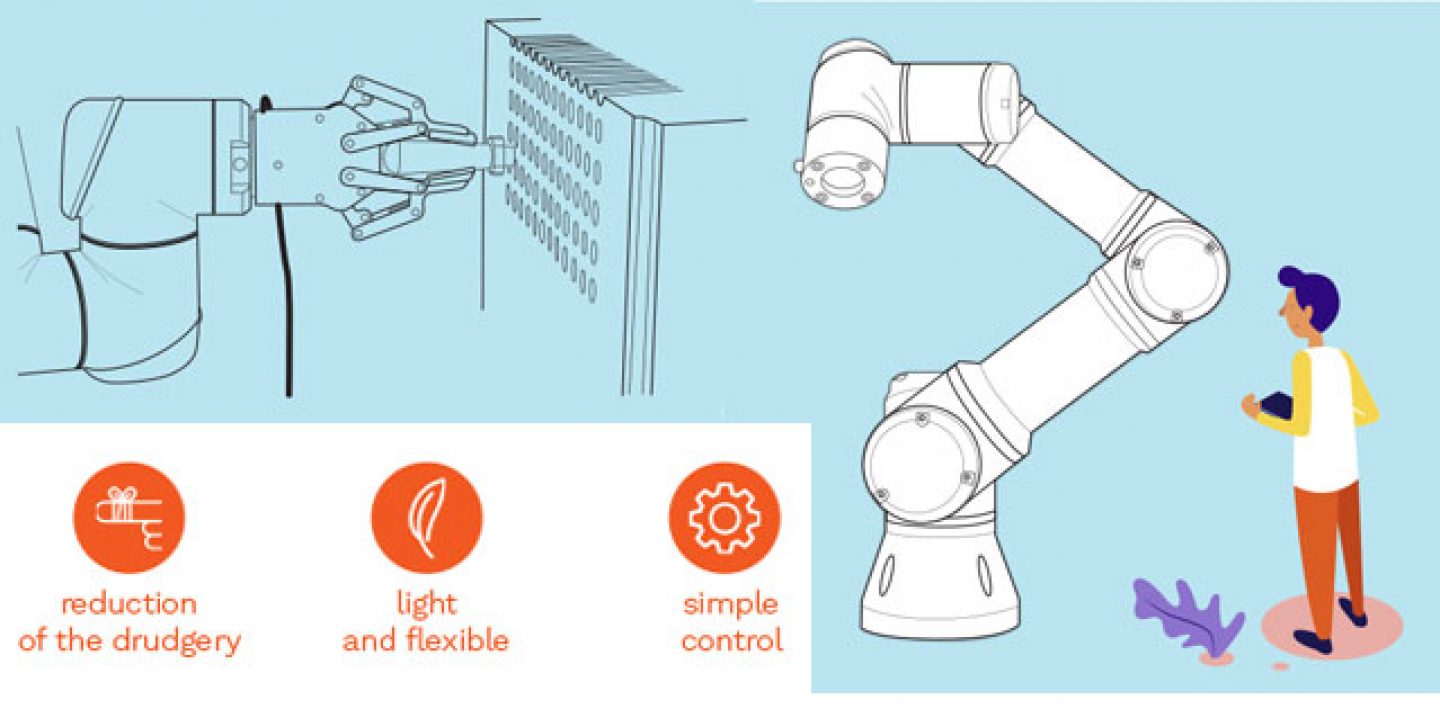
Cobotics
FORERUNNER, the robot for optimized steam generator inspections
FORERUNNER* is a light, mobile robot. Its spider-like movements in all working positions, on horizontal or vertical tubesheets, easily adapt to different steam generator geometries.
Its size and design will minimize installation and inspection times by providing improved access to the steam generator tubes for inspection and repair as required.
Installed and removed with a motorized carriage, the robot engages with the tube and walks out using pneumatically actuated grippers with fail-safe logic.
The entire process is managed remotely, via a single controller and cable, resulting in no human interface and a 30% reduction in dose.
FORERUNNER can reach more than 200 tubes in a given stance.
*FORERUNNER is developped and manufactured by INETEC (Institute for Nuclear Technology)
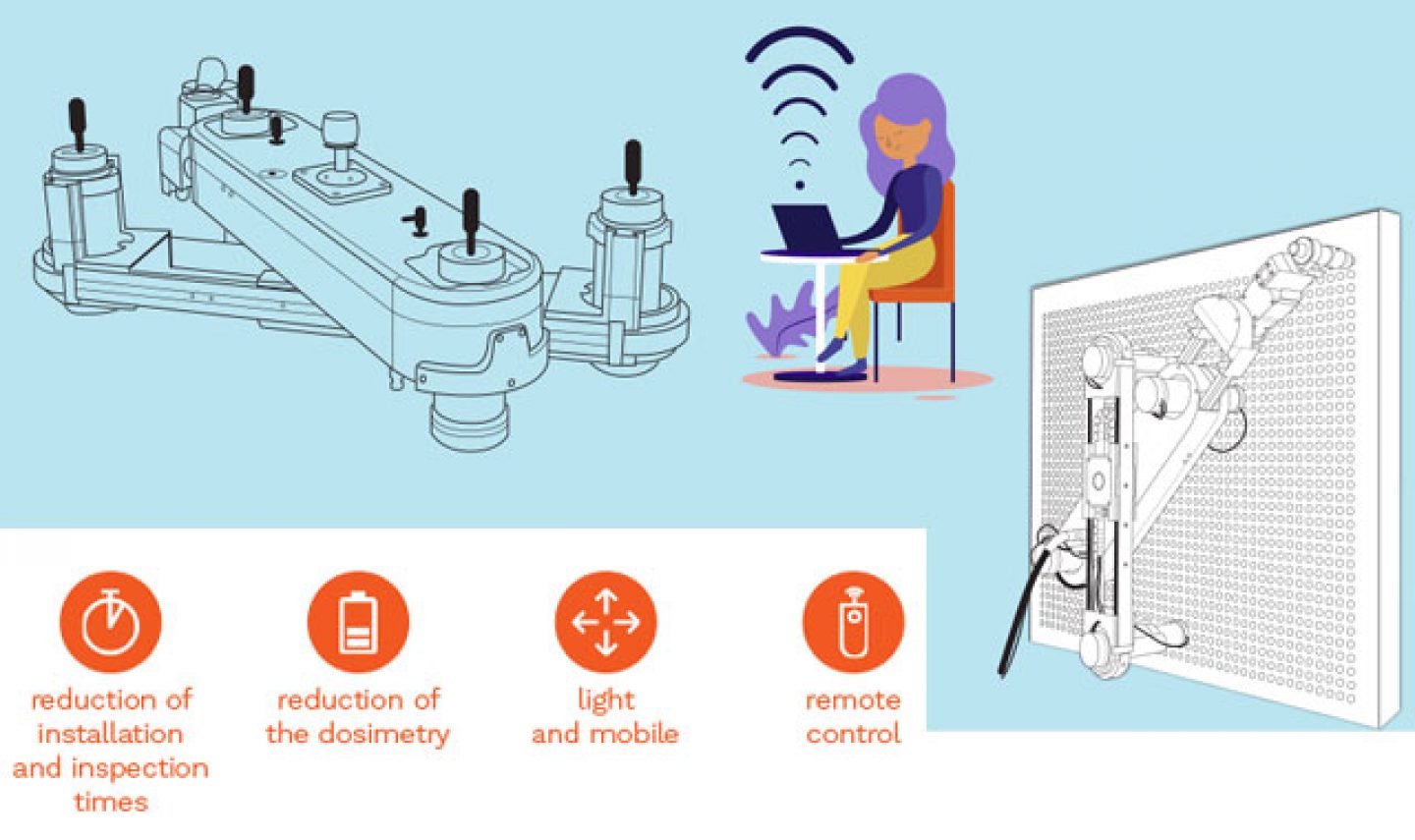
Forerunner
Éloise robot
The robot Éloise is an innovation designed by Framatome for dismantling the SuperPhenix reactor vessel*, SuperPhenix being the largest nuclear reactor currently under decommissioning in the world.
Specially designed by the Framatome teams, robot Éloise has been used to carry out cutting operations on 26 penetrations (pipework elements adjoining the primary vessel) located beneath the SuperPhenix reactor vessel slab. The purpose of this operation was to eliminate the residual sodium in order to guarantee optimum gas distribution in the vessel during the carbonation phase.
Derived from the laser robot Charli, also designed by Framatome, Éloise is a new generation equipped with 2 cameras and a specific, lightweight orbital laser head.
Cutting work on the reactor vessel is going ahead with the aid of teleoperated robots and tools.
* SuperPhenix reactor vessel
1,200 t | 25 m in height | 20 m in diameter | 3600 m3 of sodium contained in the inox reactor vessel
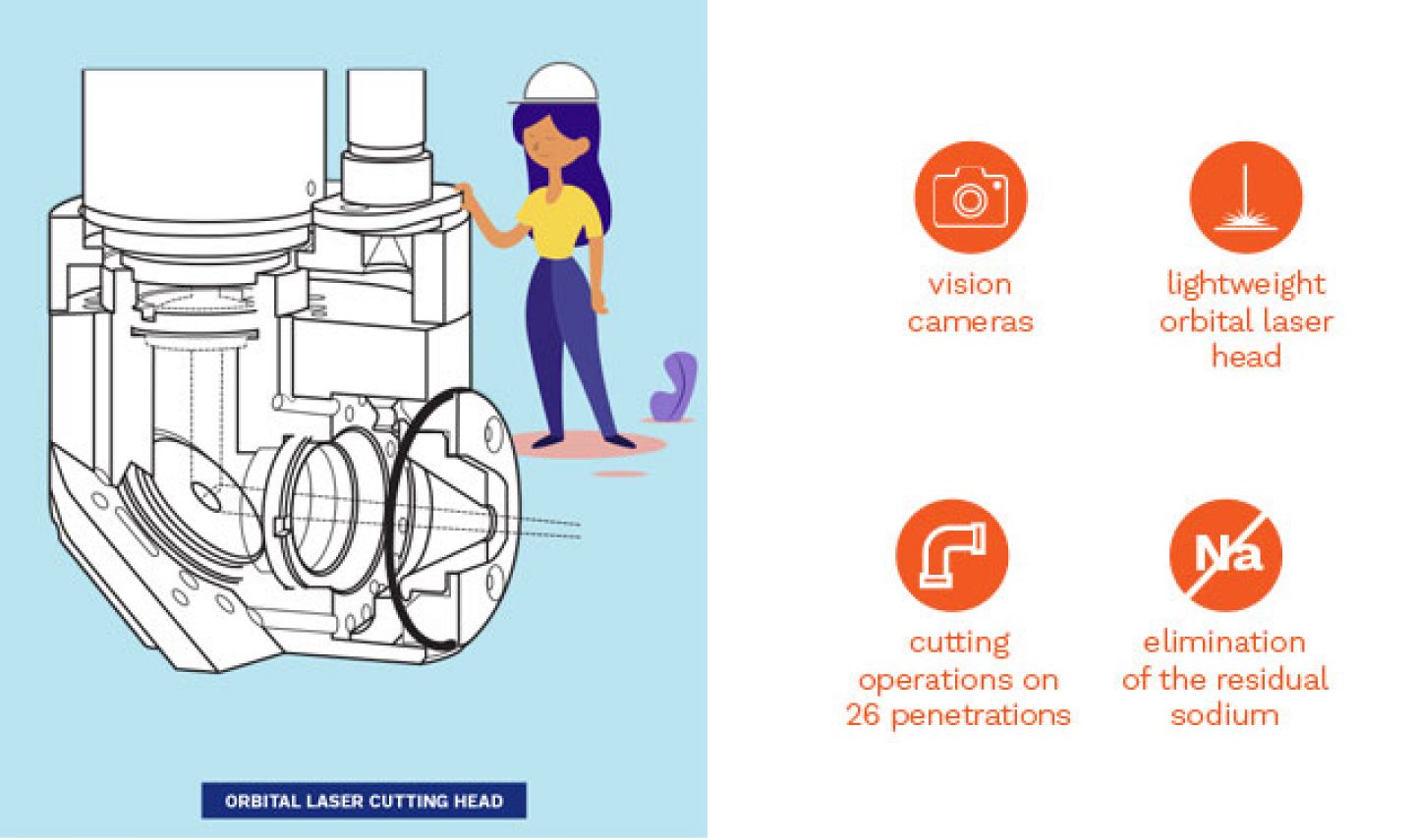
Éloise Robot
Charli robot – It even goes where you don’t expect it!
Specially designed by Framatome teams, the robot Charli is capable of working inside confined pipework structures and withstanding very harsh environments – with high temperatures, high levels of radiation and high concentrations of sodium and argon.
Equipped with vision cameras and a robotic arm carrying a laser cutting head, this supercompact ROV (remote operated vehicle) has distinguished itself by performing cutting operations on pipework inside the SuperPhenix reactor vessel, SuperPhenix being the largest nuclear reactor currently under decommissioning in the world.
The cuts, in some cases through thicknesses of 10 cm or more, have been performed on interconnection piping between the primary pumps and the base frame, so that residual sodium not removed by draining under negative pressure could be recovered.
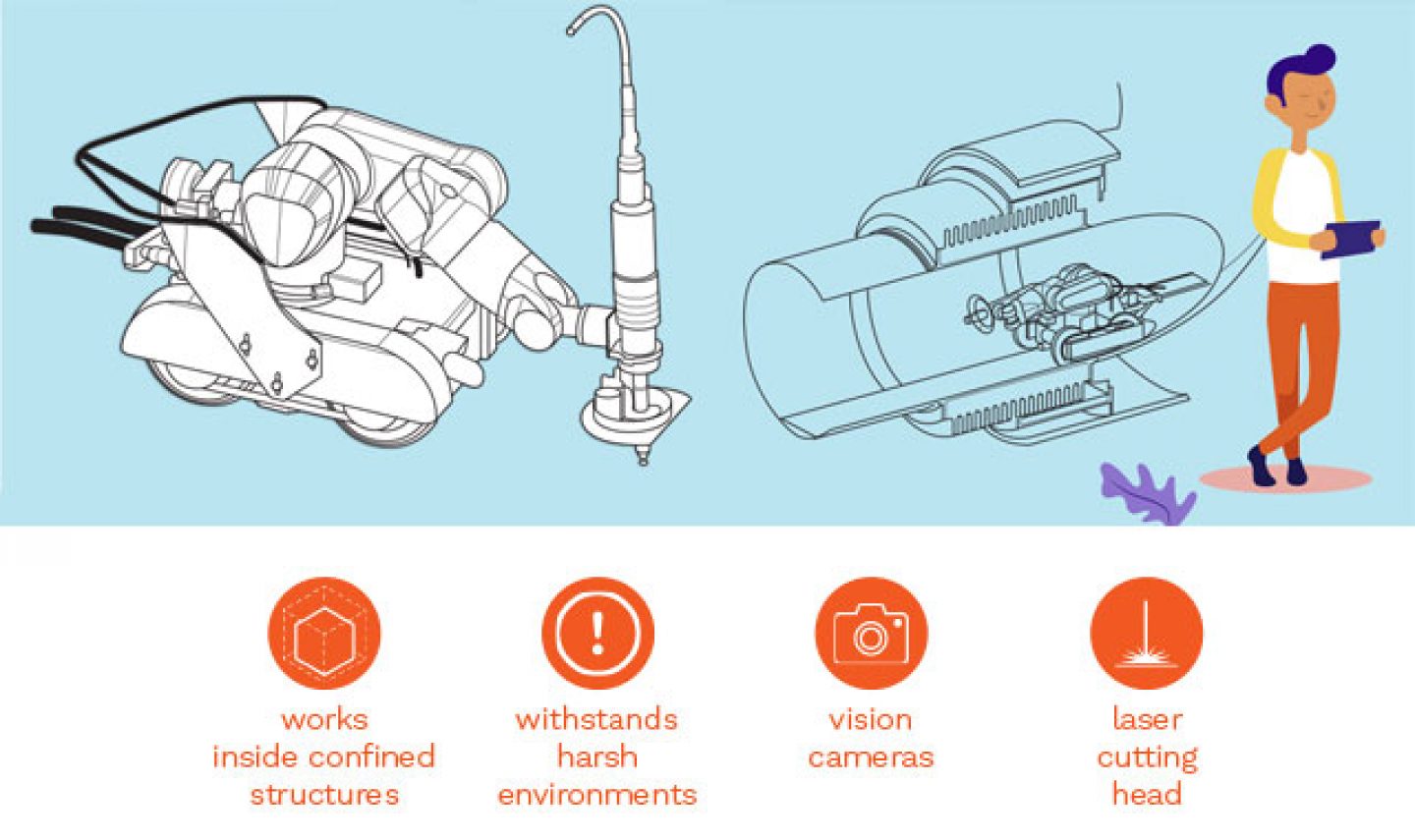
Charli Robot
Press Release
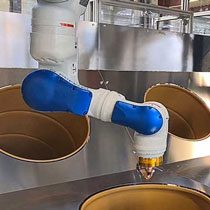
Framatome achieves milestone in robotics project for dismantling and decommissioning